In today's industrial manufacturing, industrial robots are everywhere, replacing humans in many heavy, repetitive, or otherwise mundane processes. Looking back at the development of industrial robots, the robotic arm can be considered the earliest form of industrial robot. It mimics certain functions of the human hand and arm, performing automated tasks such as grabbing, moving objects, or operating tools according to fixed programs. Today, industrial robotic arms have become an essential part of modern manufacturing systems.
What is a Robotic Arm Composed Of?
Common types of robotic arms include Scara, multi-axis robotic arms, and collaborative robots, widely used in various aspects of life and work. They mainly consist of the robot body, control cabinet, and teaching pendant. The design and manufacturing of the control cabinet are crucial to the robot's performance, stability, and reliability. The control cabinet includes both hardware and software components. The hardware part comprises power modules, controllers, drivers, sensors, communication modules, human-machine interfaces, safety modules, and more.
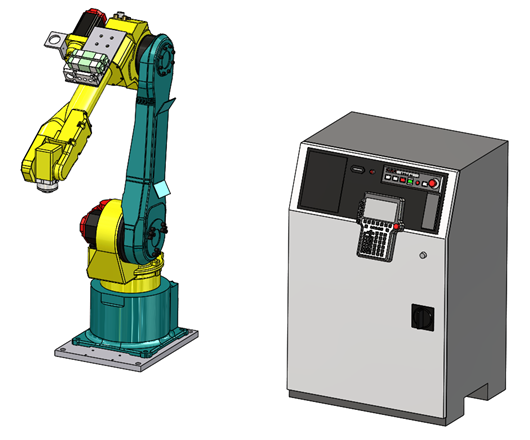
The Controller
The controller is the core component of the control cabinet. It is responsible for receiving instructions from the operator or automated system, calculating the robot's movement trajectory and speed, and controlling the robot's joints and actuators. Controllers typically include industrial PCs, motion controllers, and I/O interfaces. Ensuring the robotic arm's "speed, precision, stability" is a critical performance evaluation criterion for controllers.
APQ's magazine-style industry controller AK5 series has significant advantages and features in the practical application of robotic arms.
Features of the AK Industrial PC:
- High-Performance Processor: The AK5 uses the N97 processor, ensuring powerful data processing capabilities and efficient computation speed, meeting the complex control requirements of robotic arms.
- Compact Design: The small size and fanless design save installation space, reduce operating noise, and improve the equipment's overall reliability.
- Strong Environmental Adaptability: The AK5 industrial PC's resistance to high and low temperatures allows it to operate stably in harsh industrial environments, meeting the demands of robotic arms in different work scenarios.
- Data Security and Protection: Equipped with supercapacitors and power-on protection for the hard drive, it ensures that important data is effectively protected during a sudden power outage, preventing data loss or damage.
- Strong Communication Capability: Supports the EtherCAT bus, achieving high-speed, synchronized data transmission to ensure precise coordination and real-time response among the robotic arm components.
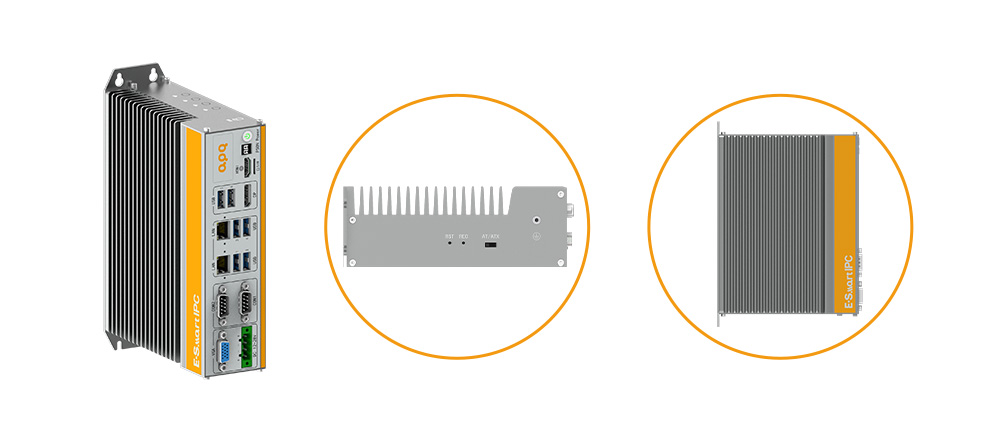
Application of the AK5 Series
APQ uses the AK5 as the core control unit to provide customers with a complete application solution:
- AK5 Series—Alder Lake-N Platform
- Supports Intel® Alder Lake-N series mobile CPUs
- One DDR4 SO-DIMM slot, supports up to 16GB
- HDMI, DP, VGA three-way display output
- 2/4 Intel® i350 Gigabit network interfaces with POE functionality
- Four light source expansion
- 8 optically isolated digital inputs and 8 optically isolated digital outputs expansion
- PCIe x4 expansion
- Supports WiFi/4G wireless expansion
- Built-in USB 2.0 Type-A for easy installation of dongles
01. Robotic Arm Control System Integration:
- Core Control Unit: The AK5 industrial PC serves as the control center of the robotic arm, responsible for receiving instructions from the host computer or interface and processing sensor feedback data in real-time to achieve precise control of the robotic arm.
- Motion Control Algorithm: Built-in or external motion control algorithms control the robotic arm's movement trajectory and motion accuracy based on preset path and speed parameters.
- Sensor Integration: Through the EtherCAT bus or other interfaces, various sensors (such as position sensors, force sensors, visual sensors, etc.) are integrated to monitor and provide feedback the robotic arm's status in real-time.
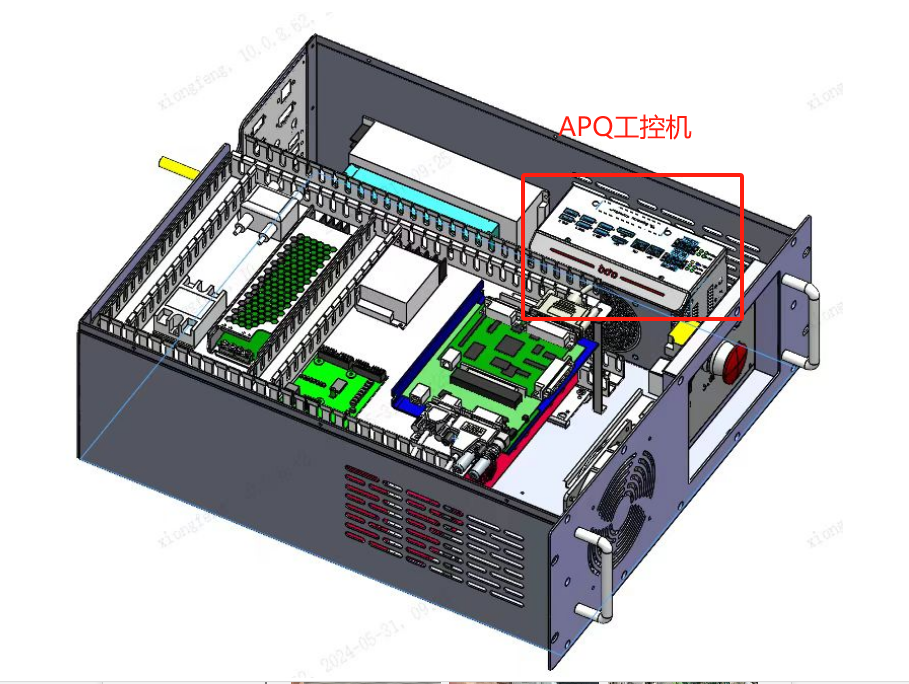
02. Data Processing and Transmission
- Efficient Data Processing: Utilizing the powerful performance of the N97 processor, sensor data is processed and analyzed quickly, extracting useful information for robotic arm control.
- Real-Time Data Transmission: Real-time data exchange between the robotic arm components is achieved via the EtherCAT bus, with jitter speeds reaching 20-50μS, ensuring the accurate transmission and execution of control instructions.
03. Security and Reliability Assurance
- Data Protection: The supercapacitor and power-on protection for the hard drive ensure the safety and integrity of data during system power outages.
- Environmental Adaptability: The high and low-temperature resistance and fanless design enhance the industrial PC's stability and reliability in harsh environments.
- Fault Diagnosis and Early Warning: Integrated fault diagnosis and early warning systems monitor the operational status of the industrial PC and robotic arm in real time, promptly detecting and addressing potential issues.
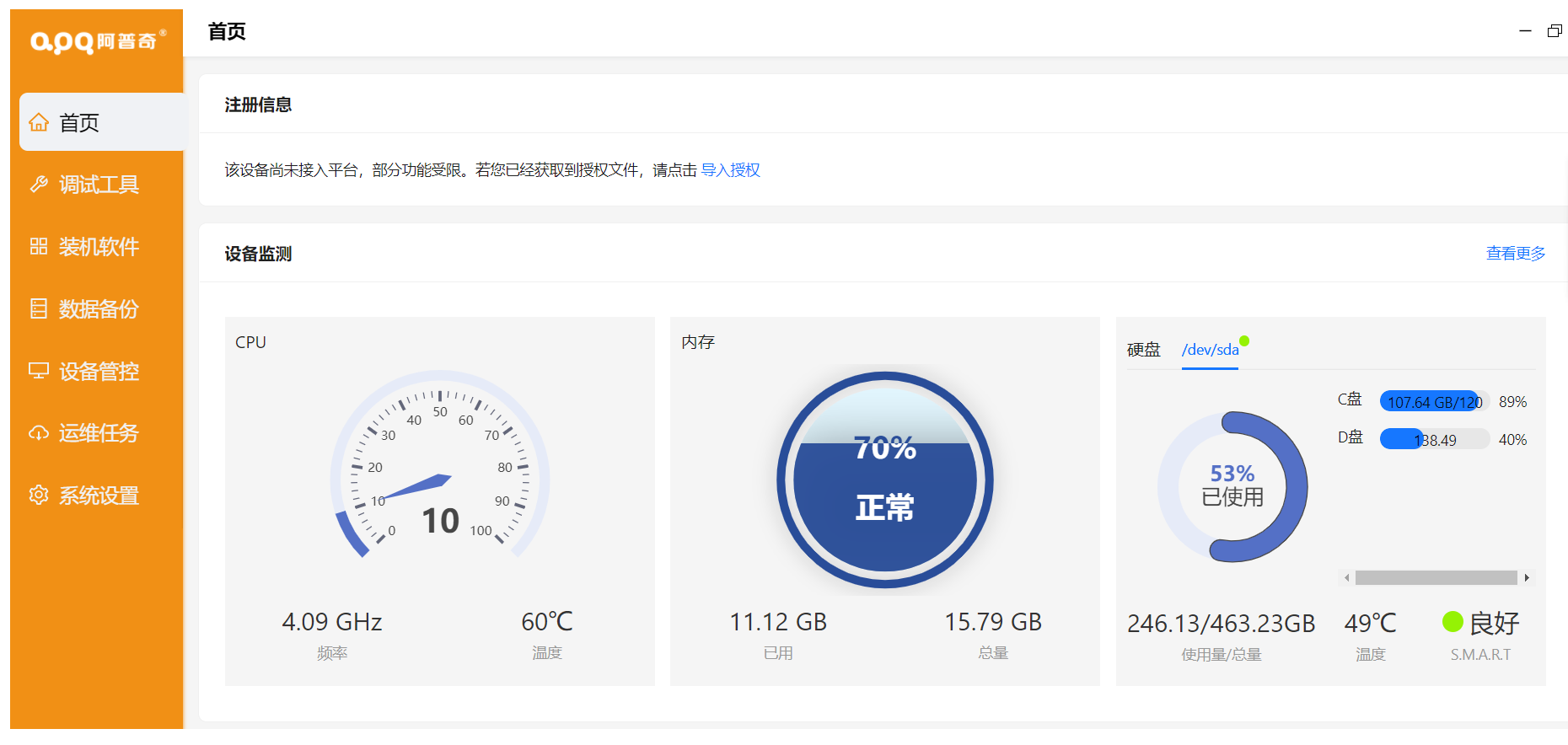
04. Customized Development and Integration
Based on the structure and control needs of the robotic arm, suitable interfaces and expansion modules are provided to achieve seamless integration with sensors, actuators, and other equipment.
APQ's magazine-style industry controller AK5 series, with its high performance, compact design, strong environmental adaptability, data security and protection, and powerful communication capabilities, demonstrates significant advantages in robotic arm control cabinets and other applications. By providing stable, efficient, and flexible technical support, it ensures the robotic arm's "speed, precision, stability" in automated operations, offering strong support for the optimization and upgrading of robotic arm control systems.
Post time: Aug-12-2024