Fonni tanishtirish
Zamonaviy sanoat avtomatlashtirishda sanoat kompyuterlari (IPCS) keskin va talabchan muhit uchun ishonchli va mustahkam hisoblash echimlarini ta'minlaydi. O'zingizning operatsiyalaringizda eng maqbul chiqish, ishonchlilik va uzoq umr ko'rish uchun IPCni tanlash uchun zarurdir. Ushbu maqolada IPCni tanlashda muhim omillar to'g'risida to'liq qo'llanma mavjud.
1. Ilova talablarini tushuning
IPC tanlovining asoslari sizning arizangizning o'ziga xos talablarini tushunishdan boshlanadi. Ishlayotgan muhit, qayta ishlash talablari va ulanish ehtiyojlari kabi omillar aniq belgilanishi kerak. Masalan, po'lat zavodlari yoki offshor platformalariga oid talabnomalar yuqori harorat, chang, namlik va tebranishlarga qodir bo'lgan qattiq dizaynlar bilan IPC-ni talab qiladi. Shunga o'xshab, AI-ga asoslangan mashinani ko'rish yoki robototexnika kabi intensiv dasturlar yuqori samarali protsessor (masalan, Intel Core I7 / i9) va GPU (masalan, nvidia). USB ,232 va Ethernet portlari kabi kerakli interfeyslarni, mavjud uskunalar va sensorlar bilan moslikni ta'minlash uchun zaruriy interfeyslarni aniqlash juda muhimdir.
Uskunadan tashqari dasturiy ta'minot talablari teng darajada muhimdir. IPC operatsion tizimingizni - Windows, Linux yoki real vaqtli operatsion tizim (RTO) -Ushbu operatsiyalar uchun zarur bo'lgan maxsus dasturiy ta'minotga mos kelishini tekshiring. Bu sanoat ish oqimiga changsiz integratsiyani ta'minlaydi.

2. Ishlash, kengaytirish va ulanish
IPC tanlovidagi eng muhim mavzulardan biridir. Vazifalaringiz, shu jumladan protsessor, GPU, RAM va Saqlash uchun zarur bo'lgan hisoblash kuchini baholang. AI, Mashinasozlik va yuqori tezlikdagi ma'lumotlarni qayta ishlashning ko'p tarmoqli ma'lumotlarni qayta ishlashiga olib keladigan, ko'p tezyurar ishlov berish va yuqori tezlikdagi ma'lumotlarni hisoblashning ko'p qismini hisoblashning ko'p tarmoqli ma'lumotlarni kamroq talab qilish uchun kamroq talab qilinadigan vazifalardan kamroq talab qilinadigan vazifalardan kamroq talab qilinadigan vazifalardan kamroq talab qilinadigan vazifalardan kamroq talab qilinadi. Bundan tashqari, kengaytirilgan xotira konfiguratsiyalari bo'lgan IPClar, masalan kengaytiriladigan xotira va saqlash kelajakda sizning ehtiyojlaringiz oshgani kabi isbotlashga imkon beradi.
Ulanish yana bir muhim omil hisoblanadi. IPClar ko'pincha sensorlar, mashinalar va tarmoqlarga ulanayotgan markaziy markaz bo'lib xizmat qiladi. IPC-ni qidirish uchun etarli I / O portlari, shu jumladan USB, Ethernet, seriya portlari (232 / Rs485) va GPIIS-ni qidiring. Yuqori tezlikdagi ma'lumotlarni qayta ishlash yoki AI arizalarida, PCEIE, M.2 yoki Mini PCie kabi kengaytirish uchun gpus, tarmoq kartalari yoki ixtisoslashtirilgan modullarni qo'shish uchun zarurdir. Ishonchli ulanish ma'lumotlarning samarali uzatilishi va nazoratini ta'minlaydigan keng sanoat tizimi o'rtasidagi chempionat va kengroq sanoat tizimi o'rtasidagi chambarchas bog'liqligini ta'minlaydi.
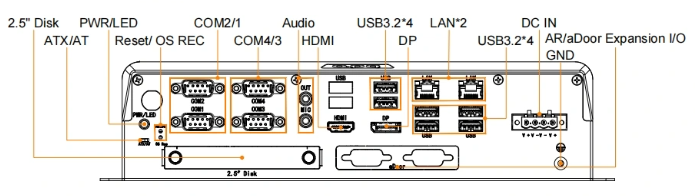
3. Chidamlilik va dizayn masalalari
Sanoat kompyuterlari ko'pincha qiyin muhitda joylashtiriladi, bu qat'iylikni muhim ahamiyatga ega. Sizning operatsiyalaringizga xos ekologik stresslarni hal qilish uchun mo'ljallangan IPC-ni tanlang. Aqlsiz dizaynlar og'ir chang bilan atrof-muhitdir, chunki ular tiqilib qolish va haddan tashqari qizib ketish xavfini kamaytiradi. Keng haroratning bardoshli (-40 ° C dan 70 ° C gacha) o'ta issiqlik yoki sovuqda ishonchli ishlashni ta'minlaydi. Shok va tebranish qarshiliki mobil yoki og'ir sanoat dasturlari, masalan, transportda yoki ishlab chiqarishda muhimdir.
Qutqaruvga qo'shimcha ravishda, IPC forma faktori muhim rol o'ynaydi. IxchamBox kompyuterlarikosmik-instaltatsiyalar uchun juda mos keladipanel kompyuterlariTasvir ekish vositalarini integratsiyalash va ularni insonparvarlik interfeysi (HMI) dasturlari uchun moslashtiradi. Markazlashtirilgan sozlamalar uchun,Rasmga o'rnatilgan IPClarServer tokchalariga oson integratsiyani ta'minlang vaO'rnatilgan IPClarMobil tizimlar uchun engil echimlar avtonom boshqariladigan transport vositalari (AGVS) kabi engil echimlar.
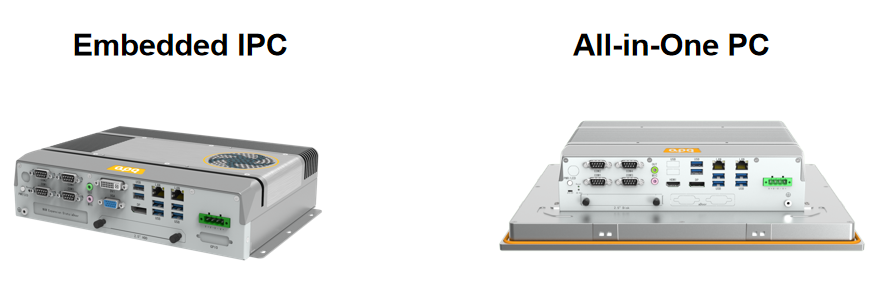
4. Xarajat, hayotiy va sotuvchilarni qo'llab-quvvatlash
Oldindan xarajat muhim omil bo'lgan bo'lsa-da, mulkning umumiy qiymati (TCO) ning umumiy narxini hisobga olish muhimdir. Yuqori sifatli IPClar uzoqroq muddatli va qo'pol dizaynlar ko'pincha to'xtash joyi va parvarish xarajatlarini kamaytiradi, muddati uzoq muddatda pulni tejashni kamaytiradi. Sanoat kompyuterlarining energiya samaradorligini baholang, chunki sanoat kompyuterlari 24 soat ishlaydi, energiya tejaydigan modellar operatsion xarajatlarni sezilarli darajada kamaytirishi mumkin.
Sotuvchi qo'llab-quvvatlash va kafolatli variantlar bir xil darajada muhimdir. Ishonchli ishlab chiqaruvchi bilan hamkorlik texnik yordam, dasturiy ta'minotni yangilash va moslashtirish imkoniyatlaridan foydalanish imkoniyatini ta'minlaydi. Sanoatning o'ziga xos ekspertizasi bo'lgan sotuvchilar, masalan, neft va gaz yoki AI va robototexnika uchun yuqori samarali ishlaydigan IPC kabi moslashtirilgan echimlarni taklif qilishlari mumkin. Kuchli sotuvchilar munosabatlari sizning IPC-ning hayoti davomida IPC operatsion va zamonaviy ravishda saqlanib qolishiga yordam beradi.
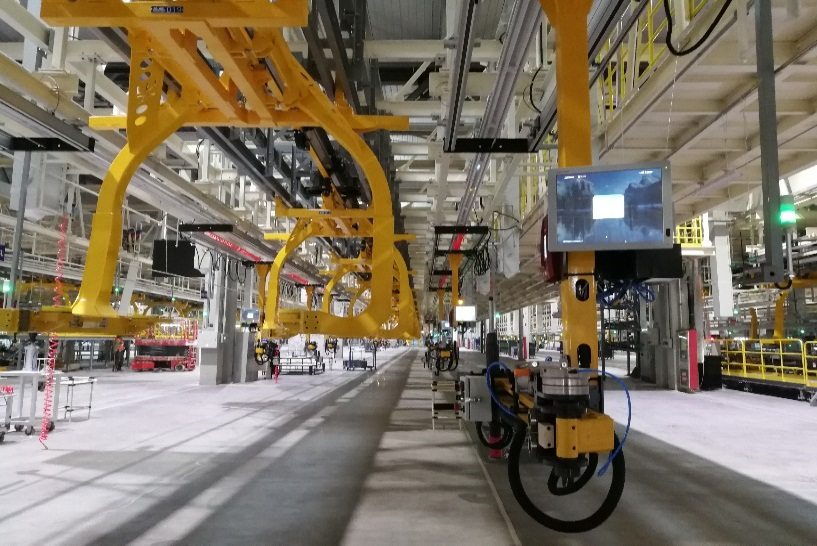
O'ng sanoat kompyuterini tanlashingiz, shu jumladan ishlash, mustahkamlik, ulanish va xarajatlar haqidagi mulohazalarni batafsil baholashni talab qiladi. O'zingiz ishonchli va samarali operatsiyalar bilan siz ishonchli va samarali operatsiyalarga erishishingiz mumkin, kelajakda sizning tizimingiz salqin va sotuvchini qo'llab-quvvatlash orqali uzoq muddatli xarajatlarni kamaytirishingiz mumkin. Sanoat kompyuterlari zamonaviy avtomatlashtirishning asosi va ehtiyotkorlik bilan tanlangan IPC hatto eng talabchan sanoat muhitida ham muvaffaqiyat baxsh etadi.
Agar siz bizning kompaniyamiz va mahsulotlarimizga qiziqsangiz, chet ellik vakilimiz Robin bilan bog'laning, Robin.
Email: yang.chen@apuqi.com
Whatsapp: +83 18351628738
O'tish vaqti: 1-dekabr, 1-2024